1. Tire Data – Introduction
TIRE DATA. Starting from the earliest design phases in automotive field, testing sessions carried out in reliable simulation environments support the product optimization considering multiple constraints and allowing to significantly reduce the number of prototypes, linked costs and required time. In such a scenario, tire-road interaction models cover a fundamental role in the vehicle’s system modeling, since the tires are accountable for the generation of forces arising within the tire-road contact patches for both vehicles handling and comfort purposes. Moreover, the tire is undoubtedly the most critical and complex sub-component of the vehicle due to its intrinsic composite structure non-linearities linked to inter-connected multiphysical phenomena.
The purpose of this paper is to analyze two different methodologies (the first one exploiting outdoor vehicle data, the second one indoor flat track tests-driven) for the testing and the characterization of tires, highlighting pros and cons of each, and comparing the results and the models identified thanks to them, for the same tire spec. The work is the result of a successful cooperation between MegaRide and Calspan.
2. MegaRide methodology for tires analysis and modeling
MegaRide, an Italian spin-off company of the University of Naples Federico II, developed since 2014 an innovative methodology to characterize tires behavior, whose conceptual features are linked to the will to adopt the vehicle equipping the tires “as a sort of moving lab”, using the standard sensors onboard of the vehicle itself, getting the objective tire/road interaction curves of the actual tires, in contact with the actual road, under the actual working conditions it will face during its lifecycle.
2.1 From vehicle outdoor data to tire-road interaction characteristics: TRICK tool
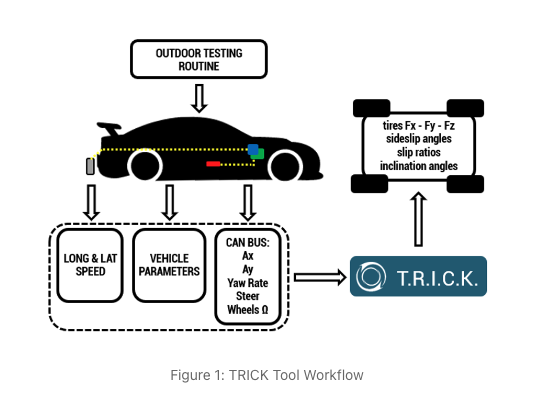
For the activity described in the current paper, track tests session has been carried out at Circuito del Sele in Battipaglia, during an outdoor experimental campaign organized within a wider project (Seaside Racing) aimed to fully characterize a vehicle, identifying and calibrating tire physical models and bringing the actual realism of experimental reality back to a simulation environment with a focus on handling, ride and comfort applications. The chosen vehicle was a Fiat 124 Spider and the tires under study were Toyo Tires Proxes R888R 195/50 R16.
The first step of the whole digitalization process implies the use of TRICK (Tire-Road Interaction Characterization and Knowledge) [1,2], a development tool to be employed in experimental outdoor activities, able to increase the amount of information that track sessions can provide and to collect data useful to identify the parameters of tire interaction models used in simulations.
The tool is based on a vehicle model which processes experimental signals acquired from the vehicle CAN-bus and from eventual additional instrumentation for the acquisition of the speed components of the center of gravity (in this specific case, S-Motion optical sensor). The model processes the input parameters and signals to calculate the forces basing on dynamic equilibrium and the slip indices on the basis of kinematic congruence equations.
The tool provides a sort of “virtual telemetry”, constituted by the acquired signals and by a number of further channels, including: wheels slip indices (slip ratio and slip angle), wheels interaction forces (vertical, longitudinal and lateral), wheels inclination angles.
One of the main features of the TRICK procedure is the possibility to get the pure and combined tire/road interaction curves. In Figure 2 an example of lateral interaction is given.
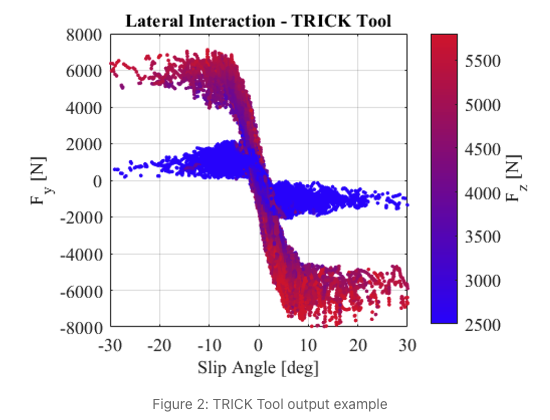
In Figure 3 it is possible to appreciate that the reproduction of forces within the TRICK tool is in good agreement with the data acquired by the Kistler Wheel Force Transducers (WFT) considering a handling test, consisting of several laps with different driving styles.
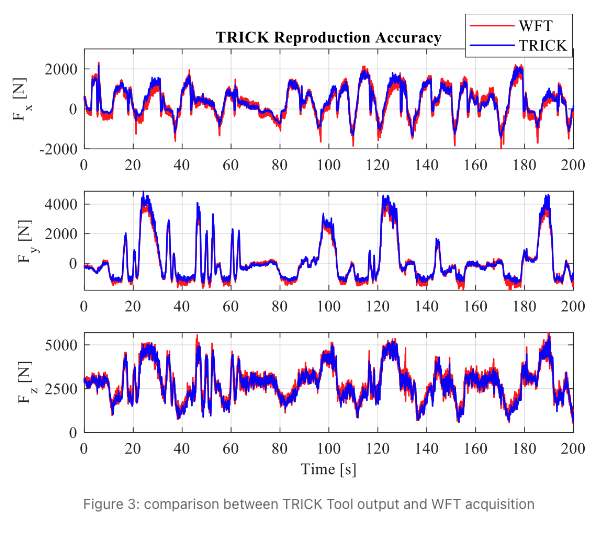
2.2 Non-destructive tire data analysis for physical models’ parameterization
In parallel to the described outdoor testing and preliminary data analysis activities, useful to the objective evaluation of the tire/road interaction experimental curves, MegaRide’s methodologies involve innovative non-destructive analysis to be performed on the tires, aimed to the parameterization of such components within the models developed for the real-time simulation of the various mechanisms (thermal, frictional, tribological, etc.) playing a role in the vehicle contact with the ground.
Tire structural parameterization consists in processing information related to tire geometric, inertial and contact patch properties in order to faithfully reproduce its behavior. Information related to geometry is directly acquired on the real tire so that a 3D mesh can be built, needed to evaluate the volume related to the heat exchanges. Tire footprints static tests are performed at a number of sample values of vertical load, camber angle and inflation pressure. The contact patch actually used for tire data models is obtained enveloping the acquired footprints and interpolating the results for different values of vertical load, inclination angle and inflation pressure.
The thermal and wear models also require a specific characterization in order to take into account of compound viscoelastic behavior, in terms of Storage Modulus and Loss Factor quantities. This is possible thanks to tests carried out through the VESevo instrumentation [3].
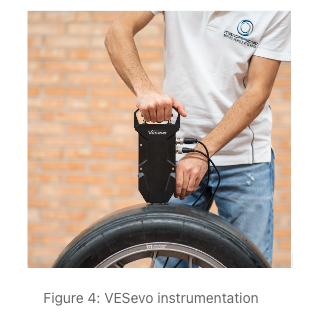
The thermodynamic model also needs the thermal properties of the layers in which the tire is radially discretized, in particular thermal conductivity, density and specific heat. They can be identified by means of an automatic error minimization procedure able to replicate tire radial temperature distribution acquired during specific indoor laser tests [4].
2.3 Thermodynamic model (thermoRIDE)
The thermoRIDE is a physical-analytical tire thermodynamic model [5,6], developed to analyze and reproduce the phenomena concerning the tire thermal behavior during its interaction with both the external environment and the inner wheel chamber (inner air, rim, brakes, etc.). It is necessary to feed the thermoRIDE model with a proper “telemetry” containing kinematic and dynamic data, such as velocities, tire-road interaction forces and slip indices, provided by TRICK tool in this case. All the information provided by the TRICK virtual telemetry is merged with data related to boundary conditions, such as external air, road and disk temperatures. Moreover, to work properly, the model needs a complete thermal, structural and viscoelastic characterization as described in the previous paragraph.
The model gives in output the circumferential and lateral temperature distribution of the different layers in which the tire is discretized along the radial direction, the tire inflation pressure and the heat exchanges.
Thanks to the experimental session carried out at the Circuito del Sele, and to the availability of specific redundant sensors as the external and internal IR thermal ones, the data acquired allowed to validate the outputs obtained by the thermal model. The comparison between acquired temperatures signals and the model outputs signals for the rear right tire can be observed in Figure 5. The model shows good accuracy in the reproduction of the actual thermodynamic behavior of the tire, as concerns external tread surface and inner liner one. Consequently, the predictions related to the inner and non-measurable layers, can be considered reliable for further analysis and for real-time simulation applications.
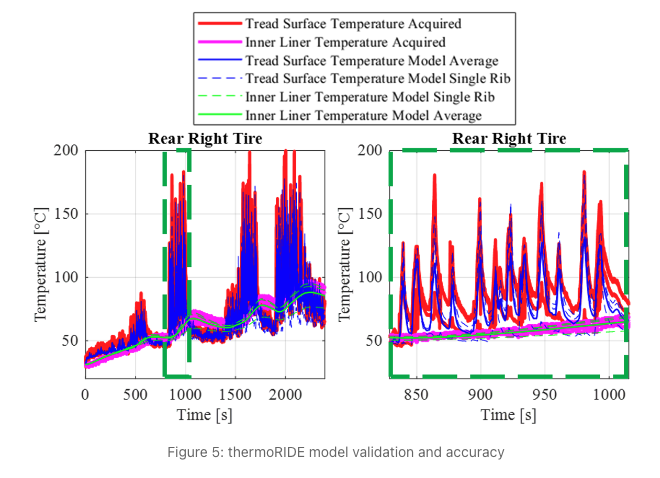
2.4 Wear model (weaRIDE)
The weaRIDE is a physical-analytical tire model, developed to study and understand all the phenomena concerning the tire wear [7,8].
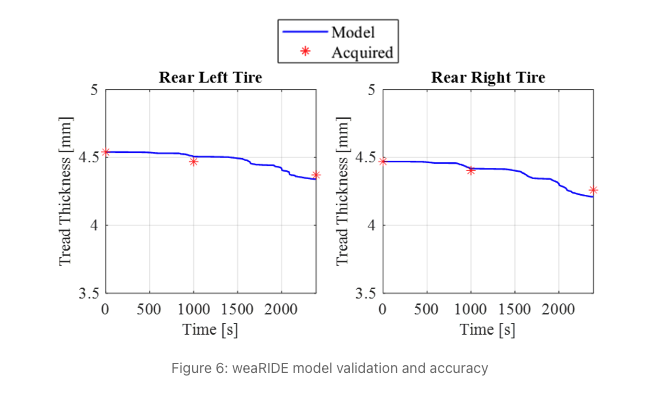
The weaRIDE also requires as input a proper telemetry, including once again kinematic and dynamic data provided by TRICK tool, and the tire thermodynamic state, in this case provided by the thermoRIDE model. The weaRIDE also needs the road roughness and a complete structural and viscoelastic characterization.
Even in this case, tread thickness profiles have been validated towards experimental data acquired on the track. The simulated tread thickness decrease for the rear tires can be observed in Figure 6.
2.5 Tire dynamic module: MF-evo (adheRIDE)
The adheRIDE model allows to take into account all the interlinked complex multi-physical phenomena occurring at tire road interface which the standard Pacejka MF formulation does not consider [9,10].
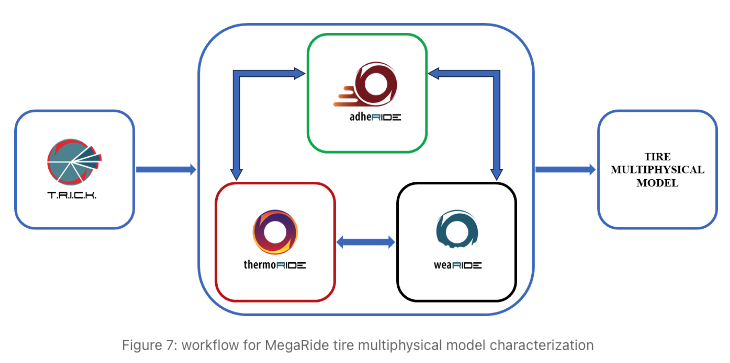
This model represents an advanced Pacejka-based interaction model, whose parameters are not static or fixed as in the original formulation, but they evolve throughout the entire run, depending on tire temperature gradient and inflation pressure (provided by thermoRIDE model) and tread thickness decrease and compound degradation effects (provided by weaRIDE model). In particular, once properly validated the thermodynamic model, a relationship between grip and stiffness towards inflation pressure and a weighted average of temperatures of tire different internal layers can be identified. The nominal MF (standard Pacejka Magic Formula) is identified in a specific range of temperature, pressure and tread thickness (usually optimal or “nominal” temperature and pressure, brand new or “pre-conditioned” tire); the MF-Evo allows to extend MF validity also far from the nominal working range, accounting for warm up and overheating conditions and for progressively worn tires.
From Figure 8 the accuracy of the fitting can be observed and analyzed. In particular, experimental points provided by TRICK tool and the identified MF characteristics in optimal conditions are plotted both for pure longitudinal and lateral interactions, for different values of the vertical load.
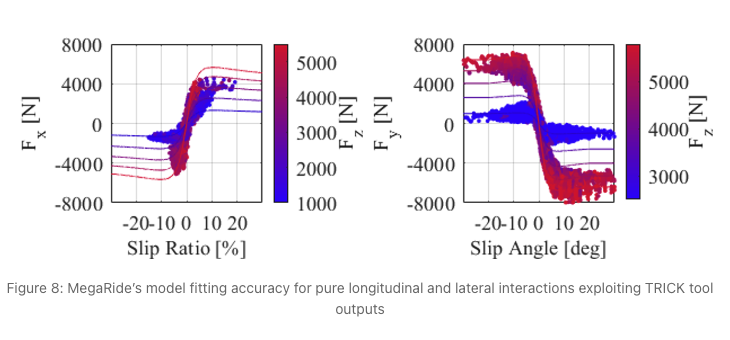
Grip and stiffness variations towards temperature and pressure observed from the experimental data and reproduced through the identified 3D surfaces can be visualized in Figure 9.
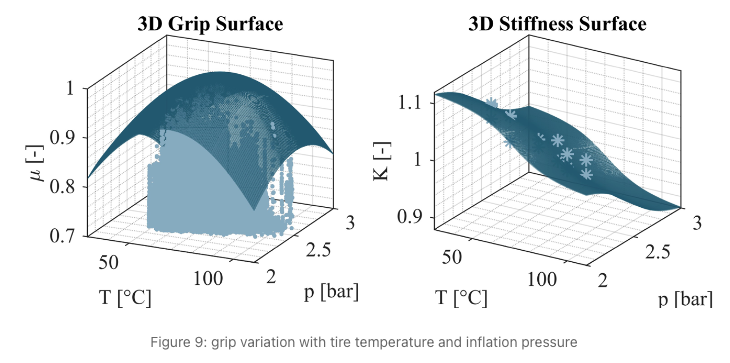
It can be appreciated how the dependency towards pressure is less pronounced with respect to the one towards temperature.
3. Calspan methodology for tire modeling
The tire data for this modeling project was collected at Calspan’s Tire Indoor Research Facility (TIRF) in Buffalo, New York, USA. This facility features a flat roadway system on which a tire data can be loaded, steered, cambered, and have wheel torque applied (braking/driving) [11]. With its proven measurement quality, accuracy, and repeatability, the facility is used by leading tire and vehicle manufacturers from all over the world for tire testing and tire modeling projects.
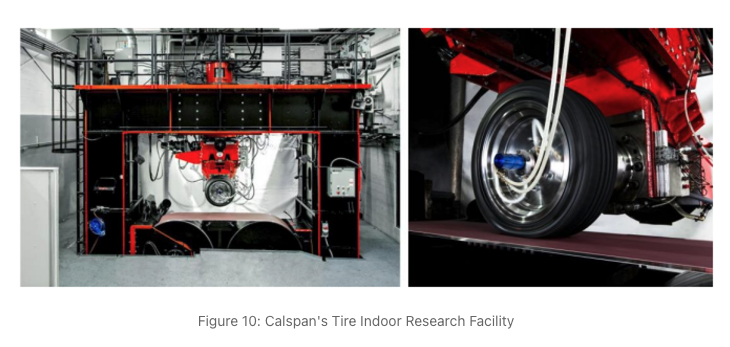
For the joint project with MegaRide, several different runs were carried out to collect the data required to fully fit a Magic Formula 5.2 tire model and to capture the thermal and pressure effects on tire performance. The details of the various test segments are presented below:
· Free-Rolling Cornering: in this segment the tire is held at a constant load and camber conditions while sweeping the slip angle in a freerolling state (no MY torque applied). The maximum slip angles and rates have been carefully controlled to reduce the impact of wear and thermal effects on the measured data. The data from the free-rolling test is primarily used to characterize the Pure FY, Pure MZ and Pure MX behavior of the tire.
· Pure and Combined Braking and Driving: in this test the vertical load, slip angle and camber are kept constant while the slip ratio is swept. The maximum slip ratio values and rates have been carefully controlled to reduce the impact of wear and thermal effects on the tire performance. The combined sweep test conditions have been derived from load and slip angle values typically seen on a vehicle. The measurements from this test are used to characterize the pure FX (using only SA=0 sweeps) and combined FX, FY, MZ behavior of the tire.
· Thermal SEL: the internal and external temperatures of the tire are measured while the tire is rolling at different conditions (camber, pressure, etc.) to characterize the heating and cooling mechanisms under pure strain energy loss conditions (without friction)
· Thermal Lat: this test characterizes the relationship between cornering stiffness and internal temperature, as well as the lateral friction coefficient versus both external temperature of the tire and sliding speed. The results are utilized to create cornering stiffness and friction maps
· Thermal Long: this test characterizes the slip stiffness versus internal temperature and the longitudinal friction coefficient versus both external temperature of the tire and sliding speed. The results are used to generate longitudinal stiffness and friction maps
· BrakeDrive Pressure sensitivity: pure acceleration, braking and combined forces and moments (F&M) test at alternative inflation pressures
· Cornering Pressure sensitivity: pure cornering freerolling forces and moments (F&M) test at alternative inflation pressures
A tire model of the type MF52 has been fit to the tire data to enable tire and vehicle simulation. The model has been fit to perform single-pressure, steady-state calculations, with smooth road contact, for FX, FY, FZ, MX, MY and MZ. The tire models were fitted using proprietary Calspan technology, using a least squares error cost function in the optimization process.
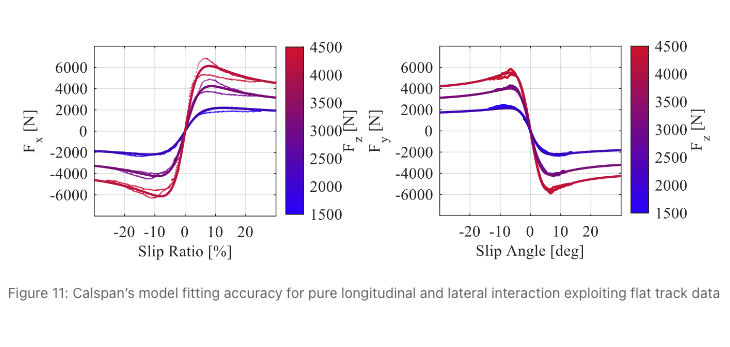
From the examples in Figure 12 the accuracy of the fitting can be observed and analyzed. In particular, experimental data acquired during indoor tests at Calspan’s Facility and model results are plotted both for pure longitudinal and lateral interactions, for different values of the vertical load.
The described methodologies were useful to characterize an empirical Magic Formula 5.2 tire model with thermal and pressure sensitivity add-ons such the cited adheRIDE model. Calspan offers additional test methodologies for other types of tire models including ride and comfort, aerodynamic, tread wear and full thermo-mechanical models.
4. Comparison between MegaRide and Calspan methodologies
Both MegaRide and Calspan methodologies aim to reproduce tire behavior as accurately as possible, to produce realistic simulations which will result in vehicle test costs savings and the improvement of vehicle control systems. The methodologies differ from each other in their testing and modeling procedures. Each methodology has its own pros and cons, as will be explained in the following section.
The first difference regards the testing method, more specifically the way tire experimental data is obtained. Calspan conducts tests in a controlled laboratory environment to evaluate tire performance under specific conditions. One benefit of using a controlled machine is the ability to decouple and independently measure all tire sensitivities. The downside of this method is that additional on-track data is necessary to correlate the peak friction and force drop-off to individual tracks. However, even basic vehicle data, such as vehicle lateral and longitudinal accelerations obtained from the CAN-bus, can be used for doing an initial correlation.
MegaRide TRICK tool uses a vehicle as a “moving laboratory” for tire testing: this allows to analyze tires behavior in real working conditions (optimal or sub-optimal) in contact with real roads. Furthermore, it is possible to explore and test tire behavior in different working conditions, such as warm-up and overheating thermodynamic phases, or worn tires, simply by asking an expert driver to perform specific maneuvers and use different driving styles. Finally, one of the most significant aspects concerning the TRICK methodology regards the possibility to assess the actual friction, stiffness, thermal and wear sensitivity to the road asphalt profile, easily measurable through optical systems. A disadvantage of TRICK tool is that the quality of tire-road interaction information is dependent on the level of detail that the vehicle characterization is able to reach.
After having made considerations about the different methodologies, it is interesting to observe model results for the same tire spec and compare them when possible. It has to be highlighted that the first and evident difference between the two procedures regards the contact counter-surface: actual tarmac for the TRICK outdoor testing sessions, reference sandpaper for the flat track test. As regards this aspect, the first allows a great flexibility in the possibility to test any kind of asphalt, the second a high level of repeatability and standardization in the procedures.
Both procedures identify the nominal Pacejka MF for modeling tire behavior in optimal conditions. From the following examples and pictures, it is possible to notice the differences between Calspan model, identified by fitting flat track data, and MegaRide model, identified by fitting TRICK tool output data. MegaRide interaction model has been reproduced at a fixed value of temperature and pressure (75°C and 2.2bar) in order to match with the conditions explored during flat track test. The Pacejka characteristics are plotted with a continuous line for Calspan model and dotted line for MegaRide model.
From Figure 12, the pure lateral interaction can be analyzed as an example. The two models show very close stiffness and similar vertical load effect on grip and stiffness. The maximum grip values are slightly higher for Calspan model, as expected due to the higher friction properties of the sandpaper. A higher shape factor is also noticeable in the Calspan model, probably due to the higher surface temperatures. Similar differences can be noticed for the longitudinal interaction.
A sub-activity was carried out to calibrate the additional dependencies of the MegaRide MF-evo using the data obtained from Calspan’s tire testing methods. The identification of the nominal Pacejka MF was easily achieved, following the exact procedure outlined in the Calspan methodology.
For the thermodynamic model, data from the Thermal SEL test was used to calibrate the Strain Energy Loss and data from the Thermal Lat and Thermal Long tests was used to determine the longitudinal and lateral friction powers, sharing factor and road conduction of the thermoRIDE, whose validation and accuracy towards an indoor test data can be visualized in Figure 13.
The data from Thermal Lat, Thermal Long, BrakeDrive Pressure Sensitivity and Cornering Pressure Sensitivity tests were used to calibrate the additional dependencies.

The difference between grip and stiffness 3D surfaces identified through outdoor and indoor tests data can be visualized in Figure 14. The main difference relies in the optimal range of tire temperature and inflation pressure, whereas the degradation of the tire performance in warm-up and overheating conditions is quite similar. The different optimal working range is expected due to the difference between flat track and real asphalt micro-roughness properties, strongly influencing the thermal behavior of the tire.
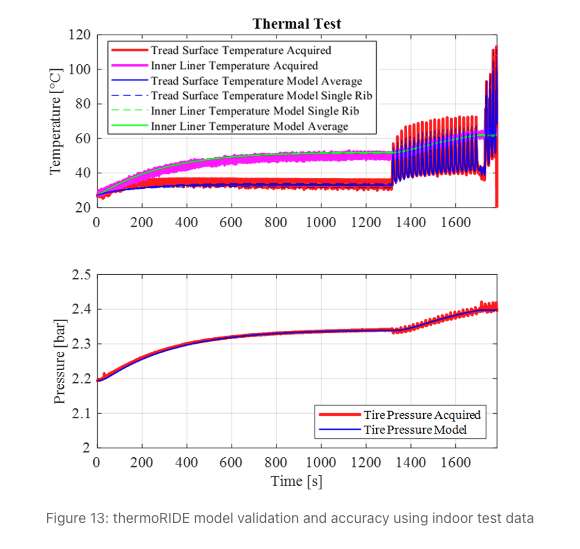
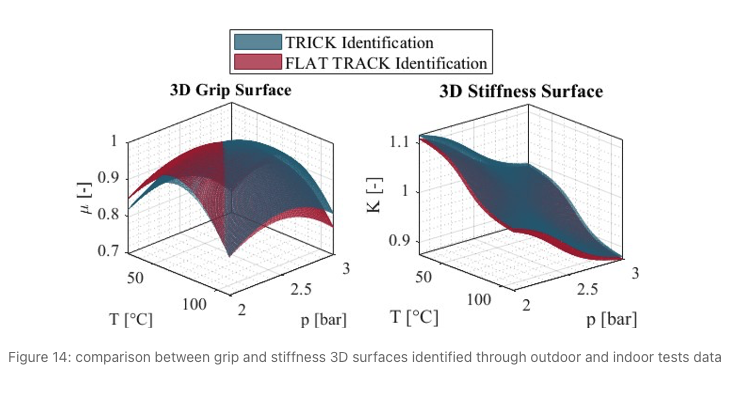
5. Tire Data – Conclusions
This paper aims to analyze two different methodologies for modeling tires, highlight pros and cons, and compare the results of the two models for the same tire data spec. Both the methodologies developed by MegaRide and Calspan have been analyzed, describing into detail each phase characterizing the whole tire digitalization process. Finally, the pros and cons of both have been discussed and the results of the identified models for the same tire data spec have been compared.
From the previous dissertation, it is possible to draw the following conclusions:
· Calspan flat road method for testing tires shows high measurement quality and repeatability, but additional on-vehicle data is required to calibrate the overall grip of the model
· MegaRide TRICK tool allows to test tires on real roads and all conditions by using a vehicle as a moving laboratory, but the quality of the data highly depends on the completeness of vehicle characterization
· Both methods, flat track testing and MegaRide TRICK tool, each come with their own advantages and drawbacks. Ideally, a combination of both would be optimal. Flat track testing works well when tire specimens can be tested in a lab, whereas MegaRide TRICK becomes the preferred choice when indoor flat track testing isn’t permitted
· In this project, both Calspan and MegaRide conducted standard Magic Formula testing along with thermal analysis. The results showed similar behavior in optimal conditions with a little higher grip for flat track testing, similar degradation of tire performance in warm-up or overheating conditions and slightly different optimal thermal windows.