Better use of data from track testing sessions can greatly improve simulation insights
One of the biggest challenges facing development engineers and testing technicians in the automotive field is the need to obtain reliable tire data, in order to understand their physical behavior. Pressure to achieve results as quickly as possible has led car manufacturers to invest ever more time and resources into tire simulation, particularly the development of physical models and analytical procedures that describe their working conditions as faithfully as possible, and that can be integrated into simulation environments.
At the same time, particularly in the motorsport world, it is necessary to consider thermodynamic effects within road contact simulations and then within the physical models reproducing interaction phenomena; a tire exhibits its maximum performance in a fairly narrow range of temperature and pressure, as these two variables mainly affect the maximum achievable grip and the tire stiffness. Research activities Experience gained thanks to the activities carried out by the University of Naples’ Vehicle Dynamics research group has led to the development of physical-analytical models that are able to predict a tire’s performance, its thermal behavior and the impact of temperature, pressure, wear and frictional phenomena on whole vehicle performance.
A tool called TRICK (Tire/Road Interaction Characterization and Knowledge)1 has been developed with the aim of processing data acquired from experimental test sessions, estimating tire interaction forces and slip indices. This tool is able to provide a sort of virtual telemetry system that feeds a specific
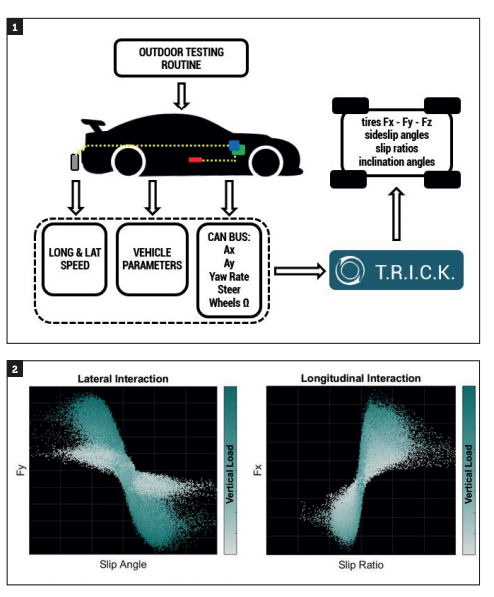
thermodynamic model which gives as an output the circumferential and lateral temperature distribution across the different tire layers. Finally, thanks to the development of a specific wear model, it is possible to calculate tire thickness variation and to evaluate its effect on tire temperature and pressure. tire simulation software
TRICK overview
TRICK is a development tool intended to be employed in experimental testing activities. It is able to increase the amount of information from track sessions and provide data which is useful in identifying the parameters for tire interaction models used in simulations.
The main uses for which this methodology has been conceived include tire characterization without bench testing, objective analysis of test sessions results, performance evaluation work and tire model parameter identification. The tool is based on a vehicle model which processes experimental signals acquired from the vehicle CANbus, with the hope that in future, additional instrumentation for the acquisition of the CG speed components can be incorporated.
For correct employment of the TRICK tool, a reliable description of the vehicle is required (geometries and masses involved). The model processes the input parameters and signals to calculate forces based on dynamic equilibrium and slip indices on the basis of kinematic congruence equations.
The tool provides virtual telemetry data, consisting of acquired signals and a number of further channels, including: wheel slip indices (slip ratio and slip angle), wheel interaction forces (vertical, longitudinal and lateral), wheel inclination angles and run distance. One of the main features of TRICK is the capability to produce pure and combined tire/road interaction curves. For example, in Figure 2, both characterizations are colored according to the vertical load, as shown in the color bar on the right.
The large volume of points provides a good overview of the effects (as the relationship between tangential and vertical forces) which play a crucial role in tire/road contact. Recently, the application field has been extended to heavy vehicles, such as truck, bus, agricultural and OTR. The TRICK4TRUCK tool has been developed as a customized version for industrial applications, catering for multi-axle vehicles and allowing tire manufacturers to obtain tire characterizations using their own trucks as a moving lab.
Thermodynamic model
The tire thermodynamic model has been developed to analyze and reproduce phenomena related to tire thermal behavior, including interactions with both the external environment and the inner wheel chamber (inner air, rim, brakes, etc.). The thermodynamic evolution of the tire system is described by the Fourier diffusion equation, applied to a three-dimensional domain.
The model takes into account several physical phenomena including heat generation due to friction and strain energy loss (SEL). Heat exchange with the external environment is also considered, which can be due to: thermal conduction between the tire tread and the road surface, thermal convection of the tread surface with external air and thermal convection of the inner liner surface with the inner air.
Finally, heat conduction between the tire nodes due to the temperature gradients is also accounted for. To evaluate the temperatures of the various layers and the inner pressure, it is necessary to feed the model with a proper telemetry stream, containing the following series of channels used for the calculation of the heat exchanges:
• Tire forces (longitudinal, lateral and vertical forces);
• Tire slip (longitudinal and lateral);
• Tire longitudinal velocities;
• Tire rotation frequencies;
• Tire inclination angles;
• Vehicle forward speed.
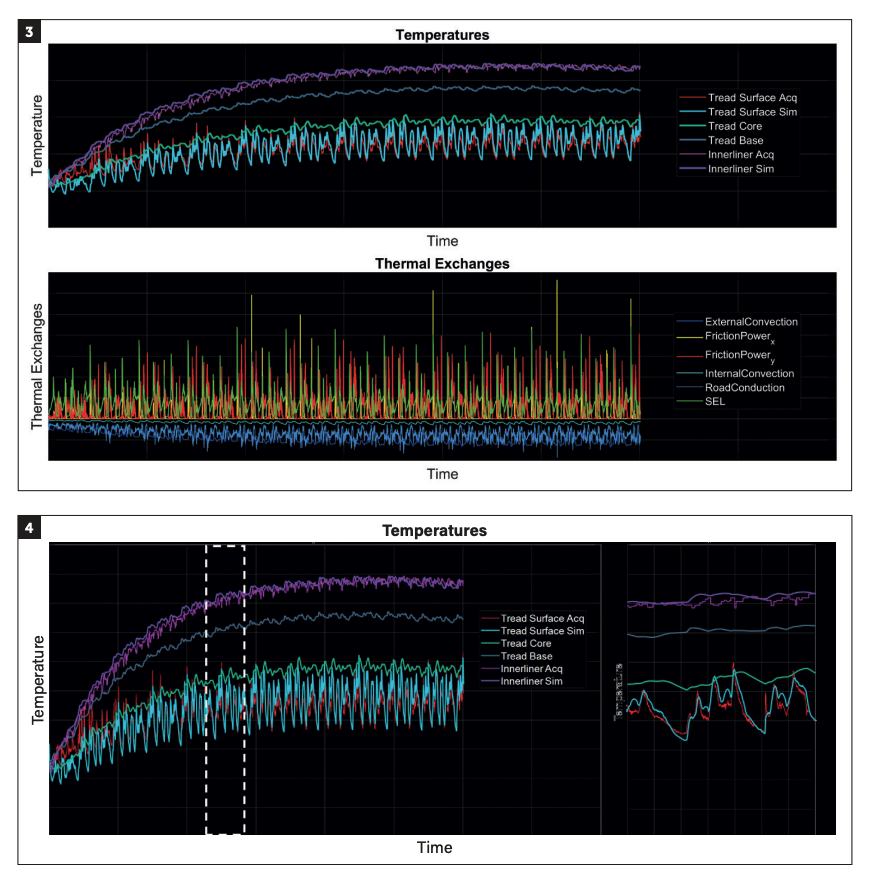
Moreover, to work properly the model has to be preliminarily characterized by means of a specific ‘Lab’ version, able to identify thermal (density, conductivity and specific heat) and structural characteristics (SEL characterization and contact patch area measurement) using totally non-destructive methodologies. The model generates an output of the circumferential and lateral temperature distribution across the different tire layers, discretized in a radial direction as follows:
• Tread surface, the outermost part in contact with tarmac and external air;
• Tread core, compound material layer, strictly connected to tire grip;
• Tread base, the deepest part of the compound layer, linked to tire stiffness;
• Carcass, the main contributor to the structural behavior of the tire;
• Inner liner, the layer in contact with the inner air.
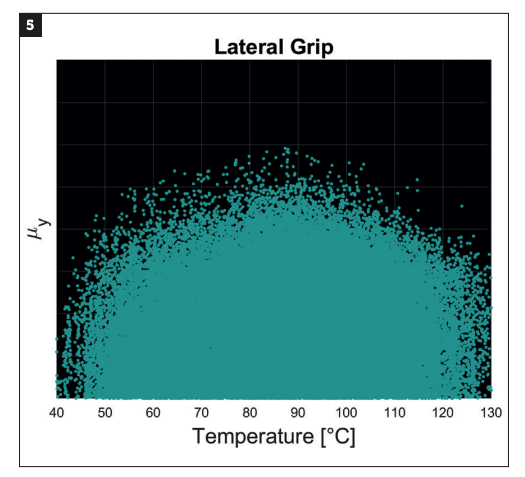
Advanced performance analysis – TIRE SIMULATION SOFTWARE
An example of the model output is reported in Figure 3. The temperatures of the multiple layers are plotted from the most external layer (tread surface) to the most internal one (inner liner). It should be highlighted that the temperature of the tread core and tread base layers are physically predicted by the model, and extremely interesting because these cannot be reached by measurement systems, and are closely correlated to global tire stiffness and to the tread hysteretic phenomena.
The model is validated with temperatures acquired via multi-array IR pyrometers, which are usually mounted at points in the tire outer layer (tread surface) and the inner liner, and from the internal pressure channel acquired by means of TPMS. Thanks to the discretization in the lateral direction (typically three ribs for cars, up to 15 for the motorcycle version) the model is able to reproduce the dynamics related to different ribs and the thermal inhomogeneities between them, created due to steering and different wheel alignment configurations.
The main advantage of the model is that, thanks to the radial discretization, it is possible to evaluate the temperature distribution in all the internal layers, which are those which most affect tire performance, especially in terms of grip and stiffness.
With the availability of internal tire layer temperature data, it is possible to obtain much more useful correlation, from which the optimal thermal range and the expected bellshaped curve can be identified. In particular, the temperature shown along the x-axis is a proper mix of the temperatures of different layers, with a significant weighting toward the tread core.
The reason why tread core temperatures offer better results can be attributed to the fact that tread surface temperature is very dynamic, and thus the polymer characteristics do not alter quickly enough to influence the whole tire’s frictional behavior. Tread core temperature is less prone to fast variations because of its intrinsic inertia and so can be easily linked to rubber viscoelastic states. Similar calculations can be conducted for the tread base layer, whose temperature is directly linked to tire stiffness and therefore variations in the tire’s structural characteristics.
In Figure 6, grip curves are plotted according to tread base temperature variation. As can be seen, the tire’s stiffness decreases as tread base temperature increases.
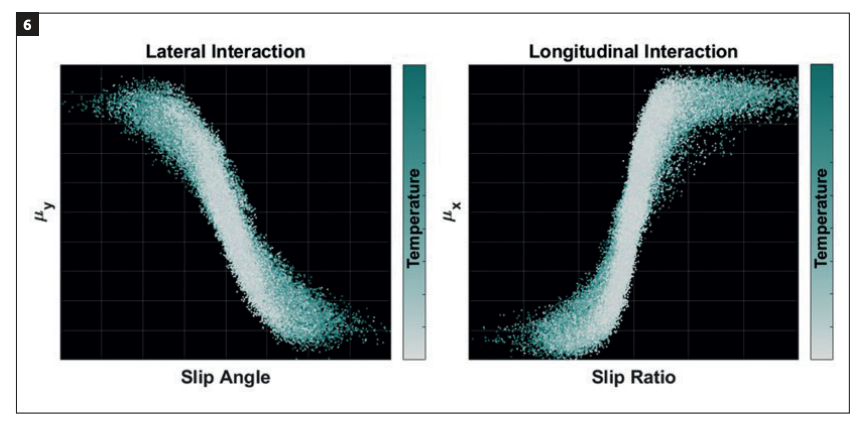
Wear model
The multiphysical approach has been recently enriched by the addition of a wear model, developed to consider wear and degradation phenomena which normally characterize the tire during its working conditions.
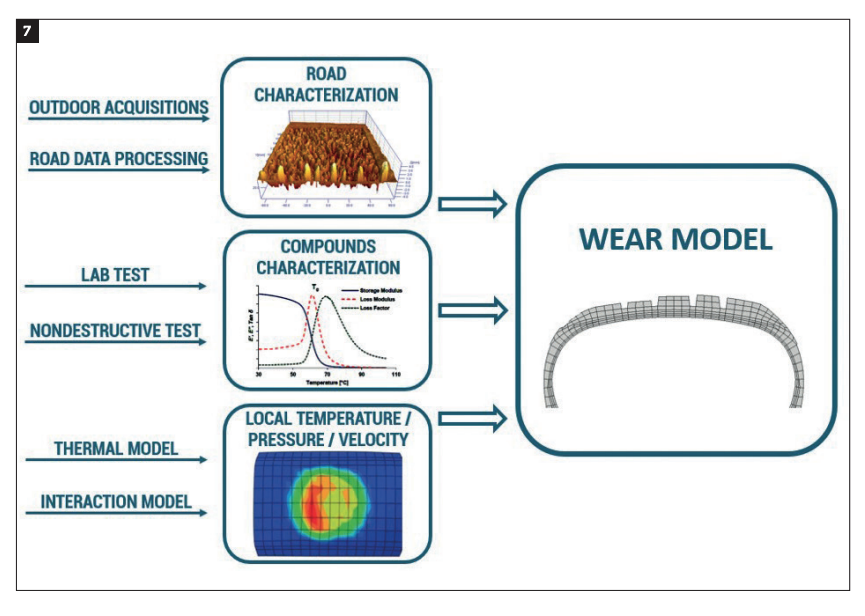
The model takes into account several factors concerning road and tire compound characterization, as well as local thermal phenomena which occur in the contact patch. Such specific modeling allows one to discern two important mechanisms: the mechanical abrasion of the compound due to interaction with track asperities, and the chemical degradation of the rubber.
The latter is due to the continuation of the vulcanization process from sustained thermal and stress cycling, which leads to a gradual hardening of the compound, and a reduction in peak friction capability. The wear model dependencies can be summarized as follows:
• Forces and sliding velocities to evaluate friction power contribution, which are available within telemetry data sets;
• Tire temperatures and pressure evaluated by employing the thermal model;
• The Storage Modulus, which characterizes the compound viscoelastic behavior and is available thanks to specific nondestructive test performed with VESevo instrumentation;
• Contact patch data, useful to take into account the local stress distribution variation.
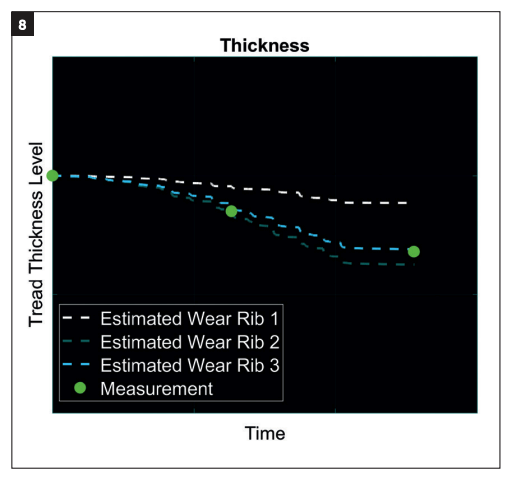
The comparison between the wear model output and the acquired data (thicknesses are measured at the end of each run stint) in terms of the residual tread thickness, is illustrated in Figure 8. An aspect of great importance is the impact of the wear phenomena on tire thermodynamics and thus on temperature and pressure profiles.
In Figure 9 the evolution of tread core, inner layer temperature and pressure is shown; the plot highlights that, after a long stint, tire average temperature tends to decrease (after a warm-up and subsequent steady phases) due to the wear effect which causes a tread thickness reduction, and a lower volume for the generation of heat for strain energy loss.
Temperature and pressure variations induced by the thinning of the tire are significant in the context of overall vehicle dynamics and form the core of the tire management strategy.
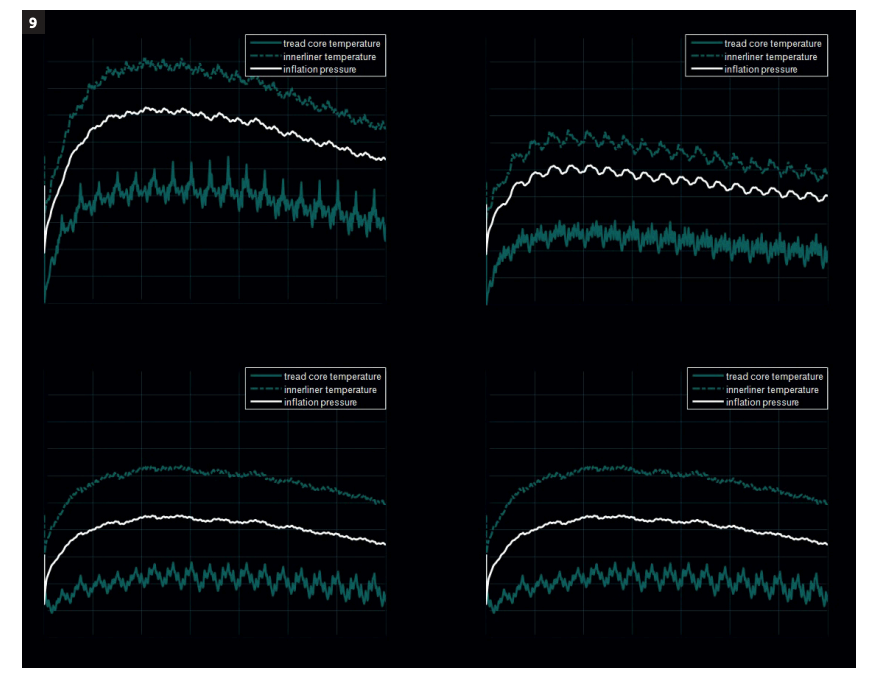
Conclusions – tire simulation software
To sum up, models, procedures and methodological cooperation can create a powerful instrument for extending the comprehension of complex themes. The TRICK tool and thermal and wear models have been successfully employed together, constituting a useful tool which can provide tire thermal analysis and be used to identify the temperature range in which grip is maximized.
Further development will concern the study of tread thickness decrease on tire dynamics; that is, how wear phenomena affects the evaluation of the performance parameters such as grip and stiffness. It is clear that this could represent an added-value instrument for the optimization of vehicle performance and setup, helping, for example, to reduce lap times in a competition setting. tire simulation software