The “Road Multiphysical Interaction Project” goes straight to its phase 2, related to the creation of the vehicle and tires multiphysical digital twins.
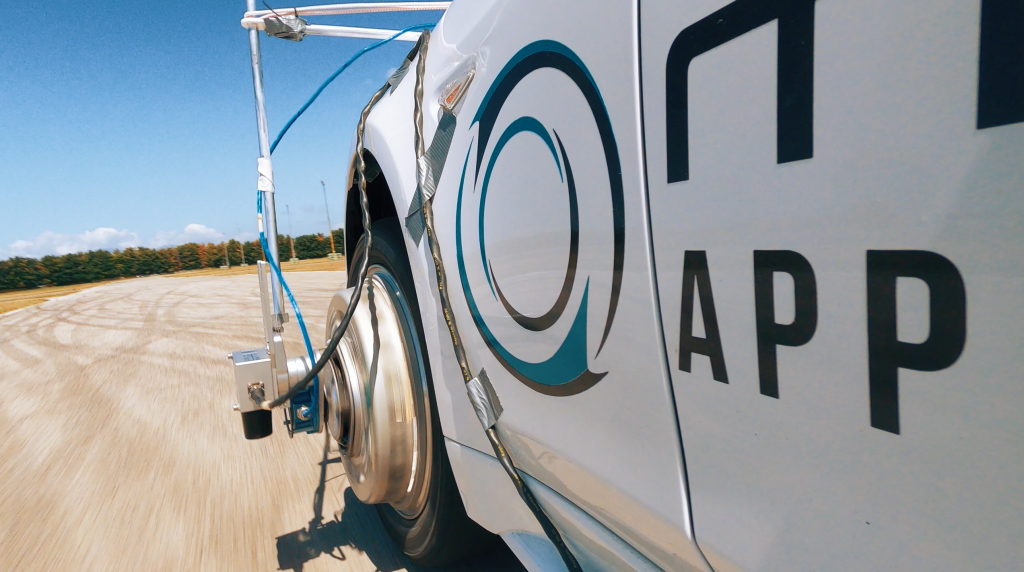
After the experimental test session, carried out at Circuito del Sele in summer with our vehicular platform, we spent the following weeks processing the huge amount of data acquired, working side by side with our partners to define the roadmap to reach the planned targets.
The R&D effort allowed us to achieve the first target of the project, involving Calspan Corporation, VI-grade, Kistler, BE CAE&Test and Almatec, interested together with our customers to work in their daily activities with new MegaRide tools enabling a progressively automated process for the parameters identification of the RIDEsuite tire physical models.
Once finalized the tools, they have been employed to:
- Process and implement the footprints data, acquired under variable load, pressure and toe/camber conditions
- Identify thermal conductivity and specific heat tire parameters, for each inner layer, obtained with completely nondestructive methodology
- Decouple the thermal and wear effects modifying the shape of the tire interaction curves, identifying the parameters to be implemented in adheRIDE model, running in parallel with thermoRIDE and adheRIDE
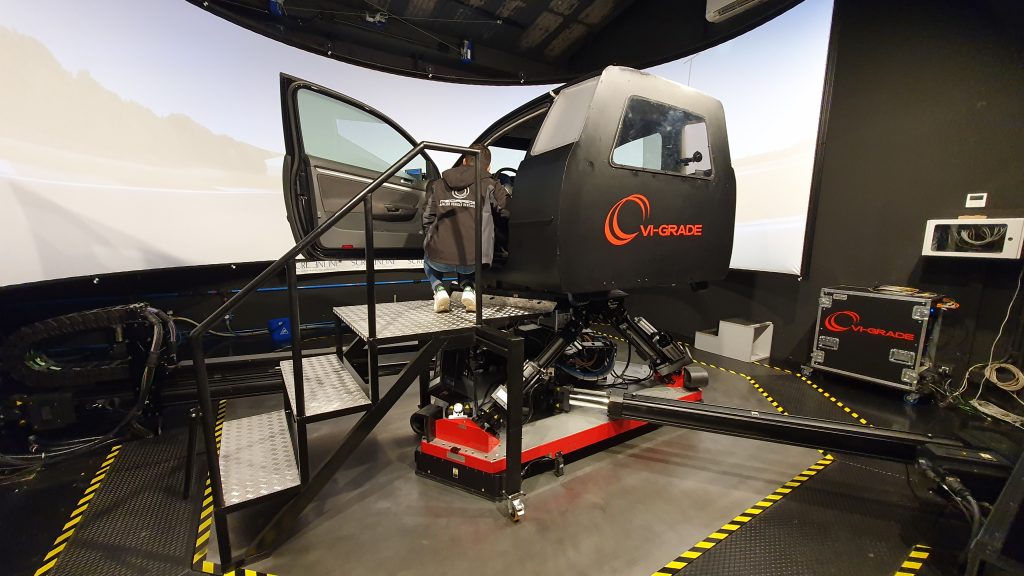
A simultaneous work has been carried out with the aim to parameterize the threedeeRIDE multicontact ride model, reaching the final target to make available to our partners, for the next step, the complete RIDEsuite tire model, comprising all the parameterized modules: thermoRIDE, adheRIDE, threedeeRIDE and weaRIDE.
With the model ready, it was turn to run it at VI-grade DIM simulators, with a subjective driving session, verifying to get back the physical sensitivities and the driver’s feelings lived in our seaside track at Sele track, virtualized by an innovative methodology hi-definition proposed by Almatec.
The first step at the DiL was to setup up the car correctly, testing different vehicle parameters to get the correct behavior and feeling; the focus was on car components which were more difficult to measure or to get precise data from the supplier, keeping the tires steady without any thermal effect active. The driver feedback and data were perfectly matching, allowing the team to reach the ideal setup pretty quickly.
The next steps were all tires related, switching-on all the physical modules (thermoRIDE, adheRIDE, threedeeRIDE) one by one to observe the car behavior and comparing it with driver feedback. Every step made the car closer to reality, with the driver more and more happy about the balance. The threedeeRIDE gave immediately to the driver the confidence to attack the kerb as in reality. thermoRIDE and adheRIDE gave him the possibility to feel the tires cold at the beginning of the simulation like they were at Circuito del Sele at the beginning of the session, with the same critical corner entry phase with snappy rear; warming up the tires had a clear effect on the lap time which was improving till few cents of second off the real pace. The synergy between thermoRIDE and adheRIDE made also possible to correctly replicate the through corner balance, with the car a bit tricky in the early entry, perfectly stable in mid corner and losing the rear in the late part of the corner.
The feedbacks from the driver and the agreement between outdoor and simulated multiphysical data encouraged all the partners of the project to keep pushing, towards next stages, regarding advanced ride models and deeper analysis focused on tire wear parameterization and effects on thermodynamics and global vehicle dynamics.
Further updates in next weeks…