VESevo, an Innovative Device for Non-Destructive and Smart Viscoelastic Characterization of Tires Compounds
Abstract – Vesevo
Viscoelastic properties of tires compound play a fundamental role into the vehicle dynamics affecting both the vehicle performances and the safety according to different working conditions depending on road roughness and temperature.
The knowledge of these properties is usually carried out by means Dynamic Mechanical Analysis (DMA) on compound samples suitable for laboratory conditions, which can be specifically produced for the test or extracted from the tire, causing its destruction. In this scenario, the Applied Mechanics research group of the Department of Industrial Engineering at the Federico II has developed an innovative device, called VESevo, capable of providing asmart and non-destructive characterization of the viscoelastic properties of tires tread compound.
The patented technology of the VESevo allows the characterization of the Storage Modulus and the Loss Factor thanks to the build-in high-accuracy sensors, which enable the user to carry out many measurements at different conditions and directly in-situ. The possibility to obtain the compounds viscoelastic response by means of a totally non-destructive and non-invasive procedure, opens scenarios of interest in a very broad panorama of applications ranging from the monitoring of the material performance during its whole lifecycle, to the quantitative analysis of products quality and repeatability of
production processes. In this work, the authors present the VESevo technology comparing the results to the ones obtained with the standard Dynamic Mechanical Analysis technique.
Keywords: Tire Materials, Non-Destructive Tire Testing, Vehicle Dynamics, Polymers, Viscoelasticity
INTRODUCTION
In automotive field, the role of the tire mechanics and physics is crucial for the optimization of vehicle stability, performance and safety. Many engineers and researchers often have to face the analysis of the mechanical and viscoelastic properties of tires to comprehend all the phenomena occurring during the tires tread-road interaction, both experimentally and in simulation.
In the last decades, compound-substrate modelling has been discussed a lot in the scientific literature and several theories have been developed to determine the frictional behavior of rubber sliding on a texture in a wide range of working conditions in terms of temperature, contact pressure, profile
roughness, etc [1, 2, 3, 4].
Despite the great effort and the notable advances made in material modeling and simulation techniques [5, 6], the study of the interaction problems requires a deep knowledge of the road roughness profiles and of the rubber viscoelastic properties, obtained thanks to several experimental campaigns [7, 8]. It is well known that, due to the complexity of the tire vulcanization process, the properties of the tread compound obtained in tire manufacturing can be significantly different from the ones achieved in the laboratory.
For this reason, the actual tread mechanical properties are complex to be determined unless the tire tread is destroyed to obtain a specimen on which the Dynamic Mechanical Analysis (DMA) is performed, which usually requires expensive machines and a long time for a full time-temperature characterization of the material [9].
Additionally, in several applications, as in the Motorsport field, tires are subjected to limitations and they cannot be tested with the classic laboratory procedures. In this context, the understanding of these viscoelastic properties thanks to non-destructive and non-invasive techniques is fundamental, in particular for some applications like polymers development for innovative compounds, road safety and vehicle performance optimization, getting more and more attention from industries and academics of
diverse areas [10, 11, 12, 13, 14]. In addition, several different techniques should be used in order to obtain the proper values of the viscoelastic properties starting from the data acquired during the laboratory tests [15,16,17].
In this paper, a pioneering instrument, named VESevo (Viscoelasticity Evaluation System Evolved), able to find tires viscoelastic properties in a non-destructive way is described. The main purpose on which the suggested methodology, based on a patented technology [18], has been developed, is the characterization of the compounds’ viscoelasticity directly on tires, with the alternative of performing the tests both in the laboratory and on track.
In this paper, following a short digression on viscoelastic phenomena, the principal features of the innovative device are displayed, as well as the processing of raw signals in order to estimate the loss factor and the storage modulus of three different tire compounds, indicated with the letters A, B and C. Finally, the obtained results are compared to
the standard DMA procedure.
VISCOELASTICITY PHENOMENON
The mechanical behavior manifested by a viscoelastic material is affected by time and temperature. In detail, it behaves half as a purely elastic and half as a purely viscous material [19]. Hence, there is a time shift between the stress and the corresponding strain, as shown in Fig. 1
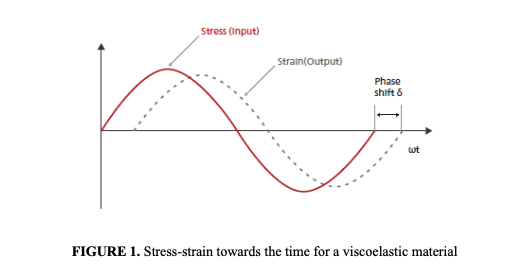
For this reason, the correlation between stress and strain is described through a complex dynamic modulus as the
amount of the total resistance to the compound deformation:
s(t)=E*=E1 +iE2 e(t)
(1)
As outlined in Eq. 1, two parts, one real and one imaginary, compose the complex module. The first one, known as Storage Modulus E1, is indicative of the material elasticity and so to its ability to store energy, the other one, defined as the Loss Modulus E2, is related to the compound’s attitude to dissipate energy as heat. As an indicator of the overall damping of the material is used the Loss Factor, which is the ratio between the Loss Modulus and the Storage Modulus.
DMA is usually applied to identify these viscoelastic properties of polymers, including the tire tread compound. Testing an adequately sized polymeric specimen within frequency range from 0.1 Hz to 100 Hz is required for this procedure [9, 20]. Fig. 2 shows typical trends of the Storage and Loss Moduli towards the solicitation frequency of the compound (referring to a constant temperature) and towards the rubber temperature (referring to a constant stress frequency.
The behavior of the compound is similar to a pure viscous solid (rubbery plateau region) at very low-frequency intervals, while at high-stress frequency values the compound behaves as a glassy solid (glassy region plateau) [21]. The same regions can be identified by analyzing the master curves towards the temperature at fixed solicitation frequency.
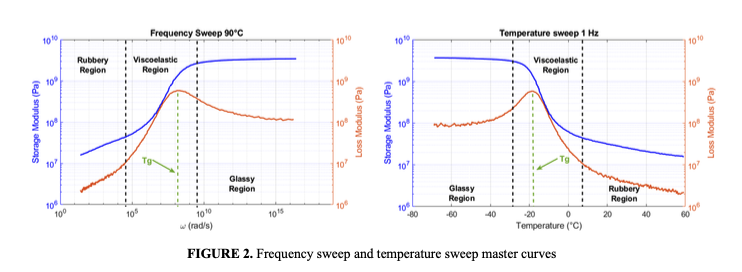
This relation between time and temperature has been firstly defined by William, Landel and Ferry [22, 23, 24] and mathematically expressed by the equation:
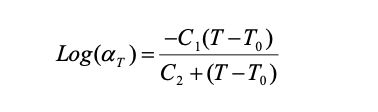

INNOVATIVE DEVICE DESCRIPTION
With the aim to propose a smart solution for non-destructive compounds viscoelastic characterization, the innovative device VESevo has been developed by the Applied Mechanics research group of the Department of Industrial Engineering at the University of Naples Federico II [25]; which allows the characterization of the tire tread viscoelastic properties and its changes caused by cooling or heating and monitoring the performances at progressive mileage or ageing depending on vehicle applications.
The VESevo can be also very advantageous for tire manufactures because it could be employed in monitoring the goodness of a huge quantity of final products in a very short time by the operators compared to the standardized procedures requiring specific and expensive test benches, as well as rolling machines or flat trac.
As depicted in Fig. 3, the VEsevo technologies include: a tool for indentation analysis, an acquisition case, necessary for the management of the acquired signals, and a self-made personalized software for raw data acquisition, developed in the LabVIEW environment to discover any acquisition anomalies and verify the goodness of an entire test session.
In Fig. 4a is shown a prototype of the VESevo device, while the functional scheme is shown in Fig. 4b. The instrument has been designed thinking to a sort of gun-shaped handles for the main purpose of guaranteeing a high level of ergonomics and stability, allowing the user to carry out many tests in the smartest procedure possible with satisfying repeatability.
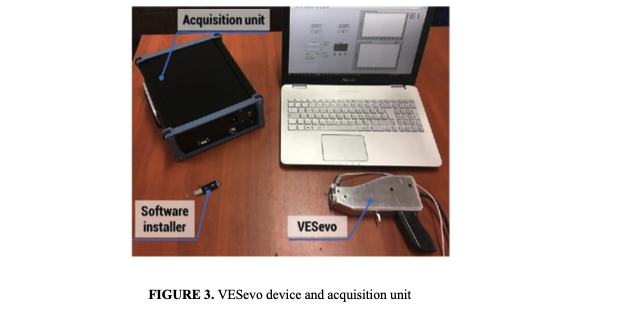
The inner structure of the device, depicted in Fig.4b, is characterized by a steel rod with a semi-spherical indenter. This rod can bounce on the analyzed material sliding inside a specific guide that consent to neglect the damping phenomena during the motion. The system is equipped with a spring so that a minimum preload is ensured. The rod begins its free drop motion always from the same starting position thanks to a semi-automatic system based on a magnet: there is a suitable slider, on which the magnet is mounted, that can hold the upper plate of the rod and I able to lift it to the maximum ascent point. This system guarantees the repeatability of the measurements.
An integrated optical sensor acquires the movement of the rod with high-frequency response, 100 kHz, and high resolution (10 μm). A compact IR pyrometer allows to acquire also the temperature of the compound during an individual test, as well as the displacement data.
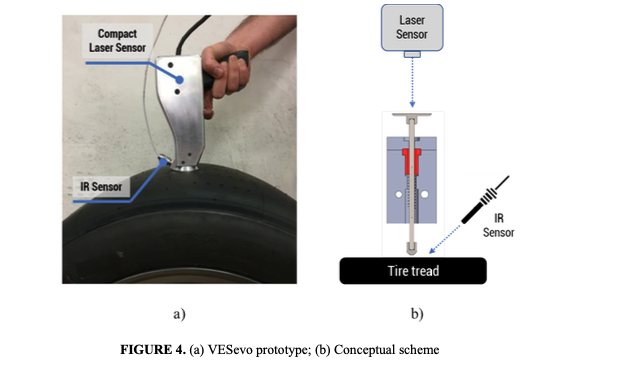
TESTING PROCEDURE AND RAW SIGNAL DESCRIPTION
In order to perform a single acquisition through the VESevo, a standardized testing procedure has been established; it consists:
- The positioning of the device vertically to the tire tread compound or slab;
- manual lifting of the indenter until a mechanical lock so that the same initial position and velocity are guaranteed for each acquisition;
- the semi-automatic system allows to release the rod when the maximum point is reached, then on the acquisition software is possible to visualize both the rod displacement curve and the compound temperature.
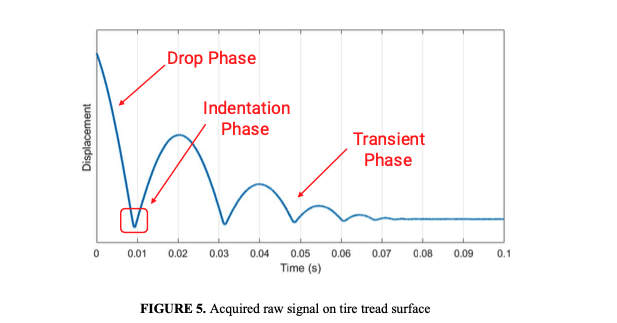
In Fig. 5, a classic displacement signal is represented. Here it can be noticed that the rod displacement exhibits different phases characterizing the motion: the phase of dropping starting from the initial position, the first indentation into the rubber thickness and, then, the transient bounce until the contact between the indenter and the tread surface is established. To explore the behavior of tread compounds as a function of the temperature, the tests can be performed changing the temperature of the sample. The testing procedure established to carry out the measurements as the temperature varies, requires that the compounds of interest have been heated or cooled and the acquisitions are made during the corresponding cooling or heating phase up to ambient temperature. Fig. 6 displays the typical raw signals acquired at different tire tread surface temperatures.
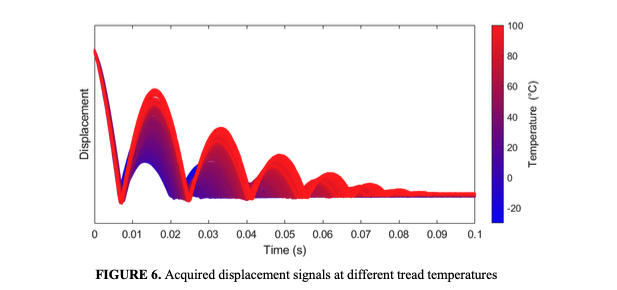
Analyzing the shape of these displacement curves, it is possible to note how the tread response changes due to temperature variations affect the motion of the rod: lower the temperature, shorter the transient phase together with bounces amplitudes. Contrariwise, increasing the temperature, the displacement reaches higher values at each bounce meaning that the compound almost behaves in a rubbery state and a lower dissipation of the rod potential energy occurs in 0.1. Here, it is worth noting that the first part of the raw signal, the drop phase, does not depend on temperature variations as this part of the signal does not involve the contact between rod and material.
VESEVO DATA PROCESSING FOR VISCOELASTIC PROPERTIES EVALUATION
The data processing aimed at estimating the viscoelastic properties of the compounds starting from VESevo measurements follows these steps:
- identification of the first contact duration between rod and compound;
- cost function optimization problem for the estimation of unknown parameters;
- viscoelastic properties evaluation from contact parameters. Preliminary to the data processing for the viscoelasticity analysis, it is necessary to identify the first contact phase between the indenter and the specimen surface after the rod drop. For this purpose, the velocity curves obtained by derivating the filtered displacement signals have to be analyzed. For explanatory purpose a characteristics velocity curve is reported in Fig. 7.
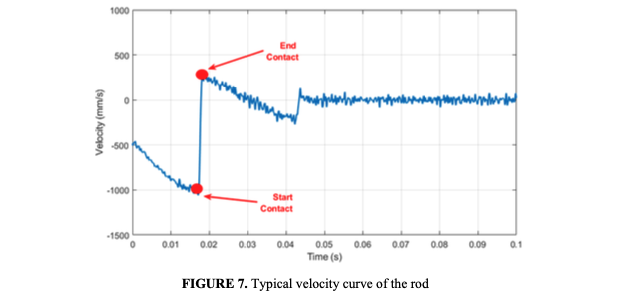
Analyzing this curve and the ones reported in Fig. 5, it is possible to identify the duration of the first contact. The beginning of the contact corresponds to the lowest value of the velocity at the end of the drop since, after that the indenter hits the compound, the absolute value of its velocity decreases until zero. This instant is the one in which the indentation depth is maximum. After that, the velocity changes sign, increasing its value until a maximum; at this instant, in which the compound stops exercising a force on the indenter, corresponds to the end of the contact.
The duration of this phase depends on the temperature of the specimen under tests. The lower the temperature, the shorter the contact duration; in opposition, if the temperature is increased, the compound behaves as a pure viscous solid and the indentation phase will be longer.
Once identified the contact duration, the shape of the displacement curve in this range can be analyzed as shown in Fig. 8.
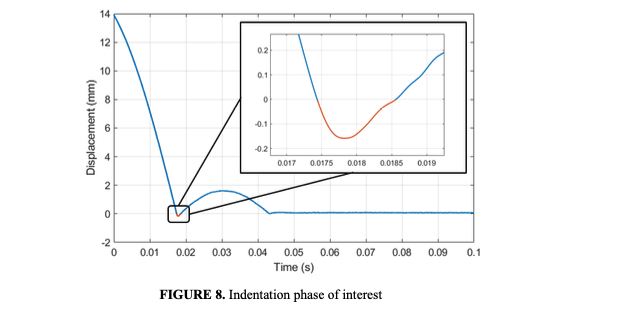
As expected from the velocity signal, the slope before the maximum indentation is different from the second phase. This is due to the fact that the motion of the rod is damped because of the interaction with a viscoelastic material. For this reason, the shape of the indentation phase can be approximated by the free-evolution of a second order non-conservative mass-spring system and mathematically described by means of the following relationship:
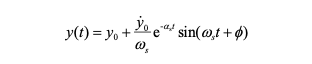
where y0 and ẏ0 are the displacement and velocity values corresponding to the start of the contact, known from the experimental measurements, ωs is the frequency of the damped motion of the rod on the viscoelastic surface, αs is
the extinction curve exponent and φ is the phase.
The parameters ωs, αs and φ can be estimated by means of an identification algorithm with the aim to minimize the following cost function:
es=y(t)-y(t),es =0.05mm (5)
where #y(t) is the experimental displacement curve corresponding to the first contact area. This cost function is optimized by means of a non-linear least-squares solver implemented in Matlab environment for each single test acquired at a certain temperature. The damped frequency values depend on the temperature at which the compound surface is during each single test. This variation is associated with the different contact duration of the indenter with the specimen, whose viscoelastic properties are different from low and high temperatures. The extinction coefficient usually exhibits almost the same trend of the damped frequency.
Once identified these magnitudes, the stiffness and the damping coefficients during the contact can be estimated through the following relationships:
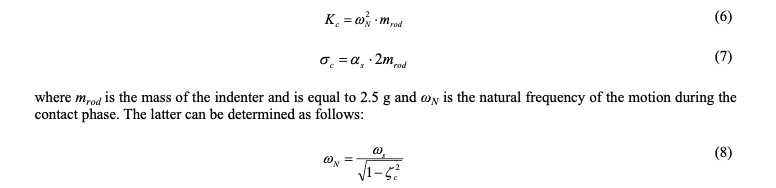
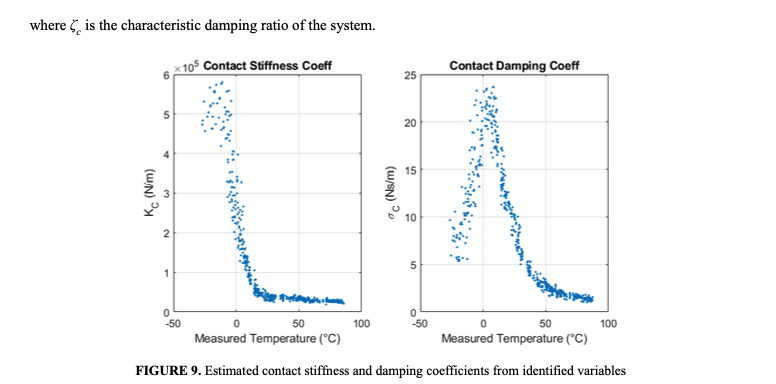
A typical trend of the contact stiffness and damping coefficient values are shown in Fig. 9. As displayed in these diagrams, these properties are function of the measured temperature because the viscoelasticity of the specimen surface on which the rod bounces.
Once analyzed these magnitudes, the Storage Modulus E1, the Loss Modulus E2 and the loss tangent tan(δ) are estimated according to the Sneddon’s theory of indentation relationships [26, 27]:
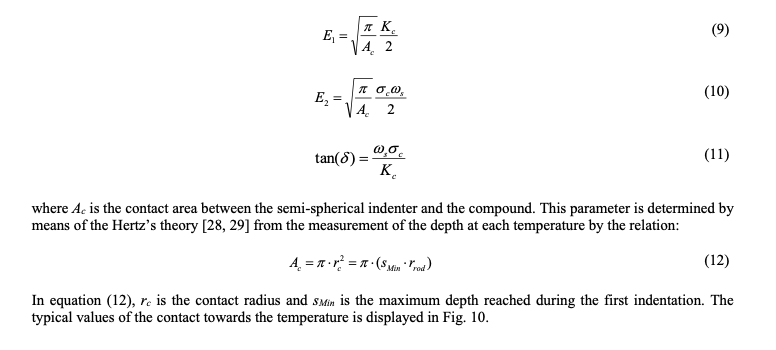
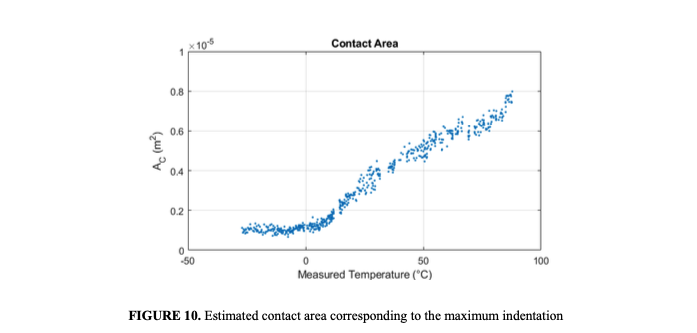
The Sneddon’s relationships do not provide directly a master curve as temperature sweep for a reference and constant frequency, as well as DMA, starting from the processing of the VESevo data. To determine the viscoelastic master curves corresponding a fixed reference frequency, each marker has been shifted according to a specific ΔT estimated by means of the William-Landel-Ferry relationship introduced in equation (2). For the results presented in the following, the shifting coefficients have been provided by a tyre manufacturer and they cannot be shared due to industrial confidentiality agreement. For the same reason, the achieved results discussed in the next section have been normalized respect to the maximum value of storage modulus and loss factor of the three tested compounds.
RESULTS
In order to validate the results carried out with the proposed non-destructive technology and the corresponding data processing, the final viscoelastic master curves have been compared to the DMA temperatures sweep at 1 Hz performed in dual cantilever configuration. For this purpose, three different tire tread compounds specimens have been tested through the VESevo in a wide temperature range and the acquired data have been processed according to the procedure described in the previous section. During the tests, the specimens have been positioned in a suitable sample-holder in order to keep stable the temperature, as shown in Fig. 11. The typical results carried out by the VESevo, shifted through the WLF relationship at reference frequency of 1 Hz, is shown in Fig. 12 for compound A. Each marker of both diagrams corresponds to a single VESevo measurement. Despite the scatter among markers, it is possible to identify a trend towards the temperature highlighting the viscoelastic behaviour of the specimen.
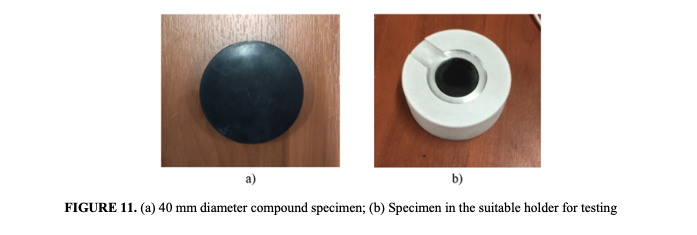
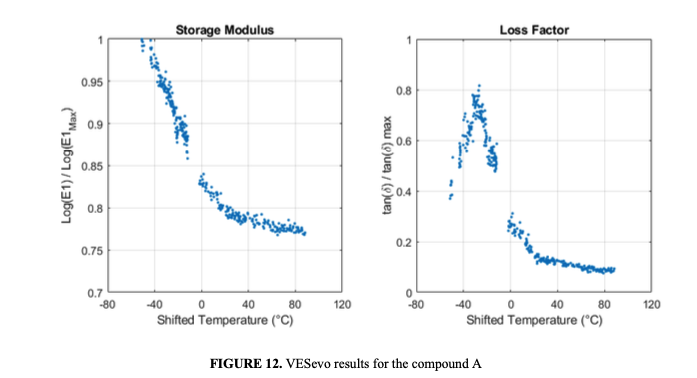
Fig. 13 displays the VESevo results of the three compounds (markers plot) compared to the corresponding DMA master curves at 1 Hz performed in dual cantilever clamp. From the figure, it is evident how the processing algorithm has been capable of identifying from the VESevo data the main trends and the values of the three compounds. Analyzing the loss factor master curves, it is noticeable how the glass transition temperatures Tg for the tested specimens are almost similar to the DMA ones. Furthermore, the VESevo results have reproduced almost correctly the full viscoelastic behaviour of these materials in the low and high temperature ranges. Another important result, highlighted in Fig. 13, is that the relative ranking among the compounds is unchanged between the two testing techniques both for the storage modulus and the loss factor. It is also possible to note that the processed VESevo data (markers) has shown that the tire C is characterized by the highest value of loss factor and the lowest storage modulus plateau at high temperatures.
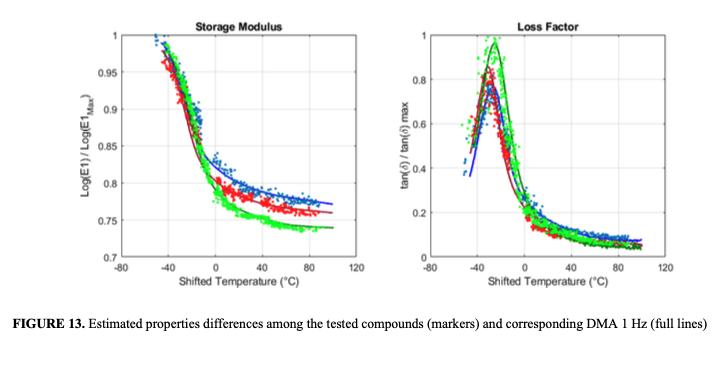
CONCLUSIONS
In this paper, an innovative prototypal device, called VESevo, and the corresponding testing procedure and data processing have been presented. This device, based on a patented technology, has been developed with the purpose of carrying out a viscoelastic analysis by means of a non-destructive and non-invasive testing approach.
The employment of the VESevo can provide a fast and smart evaluation of the viscoelasticity behavior without using expensive rheometers and specific compound samples, as traditional D.M.A. requires. Moreover, the non- invasive nature of this technique, allows that the tests can be performed on a large number of samples and an unlimited number of times; and the compactness of technology allows testing both in the laboratory and directly on track.
For these reasons, the proposed device could be open various scenarios in a wide range of automotive applications that can extend from the improvement of quality analysis in tires’ production, to the investigation of tires characteristics for motorsport applications as well as the monitoring of tires properties during the time and in different environmental conditions.
The prototype and the developed testing procedure have shown an high repeatability of the measurements and the capability of the technology in identifying the viscoelastic behavior of the compounds as a function of the temperature. The comparison between the VESevo processed data and the DMA master curves at 1 Hz has displayed that the VESevo is capable of estimating the viscoelastic properties at different temperatures and of highlighting the differences between compounds in both terms of storage modulus and loss factor.
AIP Conf. Proc. 2872, 120007 (2023)
https://doi.org/10.1063/5.0164060